Carbon deposition on catalyst in steam reforming, also called carbon formation or coking, is a major problem in petrochemical steam reforming units. It is one of the main reason of catalyst deactivation alongside with sulfur poisoning. It decreases catalyst activity or in some conditions, leads to catalyst breakage. In this article, we will review some principles of natural gas steam reforming, its conventional catalyst, causes of coking and how to avoid it.
Natural gas steam reforming
In many petrochemical plants, synthesis gas (also called syngas) is used as a feed to produce hydrocarbon products (e.g. Methanol). Synthesis gas consists of the mixture of CO, H2 and often CO2 gasses. Nowadays, syngas is mainly obtained by steam reforming of natural gas. Natural gas contains light hydrocarbons such as methane (CH4), ethane (C2H6), propane (C3H8), isobutane (C4H10) and so on. Methane has the highest composition among other components (more than 80% mole fraction).
Steam reforming is usually done by injecting steam into natural gas and directing them into two sets of reactors in series; pre-reformer and primary reformer.
Pre-reformer
Pre-reformers, which are operated at relatively lower temperature, are usually designed in the form of adiabatic fixed-bed reactors. They are responsible for reforming those hydrocarbons with more than one atomic carbon by the following endothermic reaction:
CnHm + nH2O + heat \longrightarrow nCO + (n + m/2)H2
The reaction takes place at a temperature around 500° C. Since the temperature is lower comparing to primary reformer, the following unfavorable equilibrium reactions are also happened:
Methanation:
CO + 3H2 \longleftrightarrow CH4 + H2O + heat
Water gas shift:
CO + H2O \longleftrightarrow H2 + CO2 + heat
Primary reformer
Primary reformers are operated at higher temperature of about 750° C. They are usually manufactured in the form of tubular reactors located in chamber of burners. Primary reformer’s main objective is to reform the remaining methane molecules (main portion of natural gas) by the following endothermic reaction:
CH4 + H2O + heat \longleftrightarrow CO + 3H2
The unfavorable water gas shift reaction is also happened here. The main reason of using two reforming sections (pre and primary reformers) is for removing heavier than methane hydrocarbons prior to excessive increase in temperature for methane reforming. Otherwise, we may encounter carbon deposition in primary steam reforming section, where the operating temperature is so high. It also helps reducing the size of each reactor by providing two smaller reactors in series. As a result, it guarantees a high purity mixture of CO & H2.
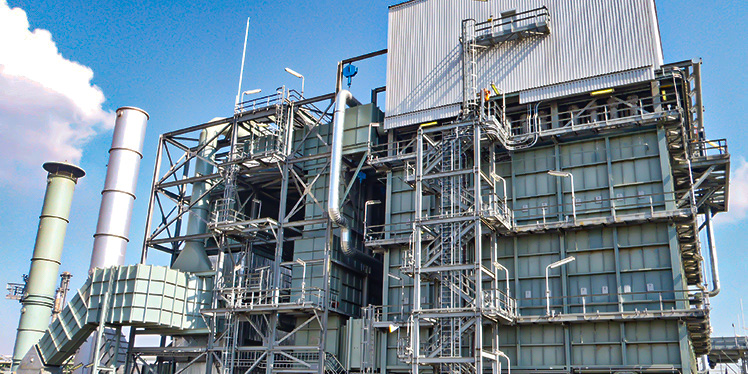
Steam reformer (courtesy of Linde Engineering Americas)
Catalyst
Nickel (Ni) is the mostly used catalyst utilized for natural gas steam reforming both in pre-reformer and primary reformer. In addition to “Ni”, there are some other metals, which can be used as active element including Co- Pd- Pt- Ir- Ru- Rh. However, nickel exhibits high activity, high stability and has reasonable price. Therefore, it is the number one choice in industry. Aluminum oxide (Al2O3) acts as catalyst support. Aluminum-based supports make nickel particles propagate evenly and with small sizes all around the catalyst surface. They are also exhibit good thermal resistance.
Pre-reformer catalysts are smaller and have more surface area due to the lower operating temperature. Pre-reformer’s catalyst is mostly supplied as pre-reduced passivated (PRP). While for primary reformer, it is supplied as metal oxide. In PRP form, only a thin layer of surface has been oxidized. Therefore, it requires lower temperature (about 250 °C) and H2 flow rate to reduce the catalyst. Whereas, for totally oxidized catalyst, it requires higher temperature (about 550° C) for reduction.

Reformer catalyst “Nickel” (4-lobe with hole), product of Johnson Matthey Co.
Carbon deposition
Carbon deposition in steam reforming reactors is so common. Cares must be taken to prevent this phenomenon. If catalysts cover with coke, they gradually lose their activity so the reaction rate becomes limited. Carbon formation occurs in two basic manners:
Whisker carbon
This type of carbon deposition forms at high temperature and has the following characteristics:
- Lift away “Ni” particles from the support surface (It forms a long whisker-like shape with the Ni particles at top)
- Less catalyst deactivation. However, may lead to catalyst breakage
Polymer gum
This type of carbon deposition forms at low temperature and has the following characteristics:
- It creates a polymeric gum at catalyst surface
- It gradually results in catalyst deactivation.
- It can Increase by introducing natural gas with higher amount of C3+ molecules
Now, let’s take a look at the most common reactions involve in carbon deposition:
Hydrocarbon Cracking:
CH4 + heat \longleftrightarrow C + 2H2
CnHm + heat \longrightarrow nC + (m/2)H2
- Higher temperature and lower pressure favor the reaction
- Mostly occurs at the end of catalytic tubes of reformer
2CO \longleftrightarrow C + CO2 + heat
- Lower temperature and higher pressure favor the reaction
- Mostly occurs at the beginning of reactor
CO + H2 \longleftrightarrow C + H2O + heat
- Lower temperature and higher pressure favor the reaction
- Mostly occurs at the beginning of reactor
Control of carbon deposition in steam reformers
There are numbers of proposed methods to prevent catalyst coking. The most important way for controlling the coking rate is to maintain the operational condition within the normal range. Temperature is a key factor, which has to be controlled within the safe range according to the operating manual. Any reformer trip or unit black shut down which leads to unwanted temperature or pressure fluctuations may result in carbon deposition. At higher operating temperature, carbon forms by hydrocarbon cracking. While at lower temperature, it forms by carbon monoxide decomposition.
Another important parameter is the steam to carbon ratio (S/C). If the amount of mixing steam, which is injected into the natural gas, is lower than the recommended value, the risk of carbon deposition will increase. In fact, high concentration of H2O increases the rate of carbon gasification by the following reaction:
C + H2O \longleftrightarrow CO + H2
At the steady state condition, rate of carbon formation becomes equal to rate of carbon gasification. Therefore, carbon will gasify as soon as it forms on catalyst surface. Consequently, the recommended methods in order to reduce carbon deposition are listed below:
- Operation at limited range of temperature
- Increasing steam to carbon ratio (up to maximum allowable value)
- Addition of potassium (K) or magnesium (Mg) promoters into catalyst structure (increase basicity)
- Operation with higher hydrogen (H2) mole fraction
- Increasing total gas flowrate to obtain a higher Reynold number. Thus, providing an enhanced heat flux distribution at catalyst surface.
Conclusion
Syngas in oil and gas industry, is used as a precursor to produce some other products such as Ammonia & Methanol. The famous technology to convert natural gas into synthesis gas is by steam reforming. Steam reformer’s catalysts are prone to coking. Therefore, controlling the rate of carbon deposition in steam reforming unit is a major challenge for all engineers and operators. However, a couple of effective practices have been proposed to eliminate this problem to some extent.
very useful thanks for writing this
If S/C more than normal operation 3.5 and temperature Moor 789 degrees. analyse outlet premary réforme CO decrisse. Need information about this
Thanks
Please be noted that due to equilibrium water gas shift reaction which is mentioned above, excessive steam may lead to lower “CO” content. Please make sure to follow licensor’s instruction in this regard.